|
Fabrication of
the Pad HPD The
fabrication of the HPD consists of a sequence of steps
Preparatory steps
All components have to be carefully cleaned
following special procedures. The sensor and readout electronics are wire bonded to the
ceramic carrier, which, in turn, is wire bonded to the feedthroughs on the baseplate.
These steps are monitiored by extensive test procedures.
The vacuum envelope and the baseplate undergo galvanic and
vacuum evaporation treatments which are essential for the cold indium sealing technique.
Aluminium pads are evaporated onto the entrance window in order to garantee a good
electrical contact to the photocathode.
Photocathode evaporation
The photocathode is produced by vacuum
evaporation of Sb, K and Cs in an ultrahigh vacuum (p ~10^-9 mbar) The evaporation plant
is baked out prior to processing to clean all surfaces and to reach a low water
contamination Various bialkali processes exist, e.g the sequential process shown above
Very god results have been obtained with a co-evaporation technique, where the Sb, K, and
Cs are partly simultaneously evaporated following a rather complex recipe. During the
processing the quantum efficiency of the photocathode is online monitored.
HPD sealing
The HPD is sealed after the photocathode
procesing applying a specially developed sealing technique which is based on a cold Indium
joint. Prior to installation in the vacuum tank, the indium metal is pre-melted and
degassed in the groove of the baseplate. A thin galvanically deposited nickel film leads
to good wettability of the surface. Also the corresponding knife edge of the envelope
flange is pre-treated accordingly. The seal is formed by joining the two components under
a force of 25,000 N as shown in the figure on the right side. |
Have a look at our online monitoring display to see what's
happening in our lab at the moment
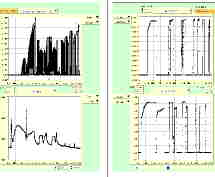
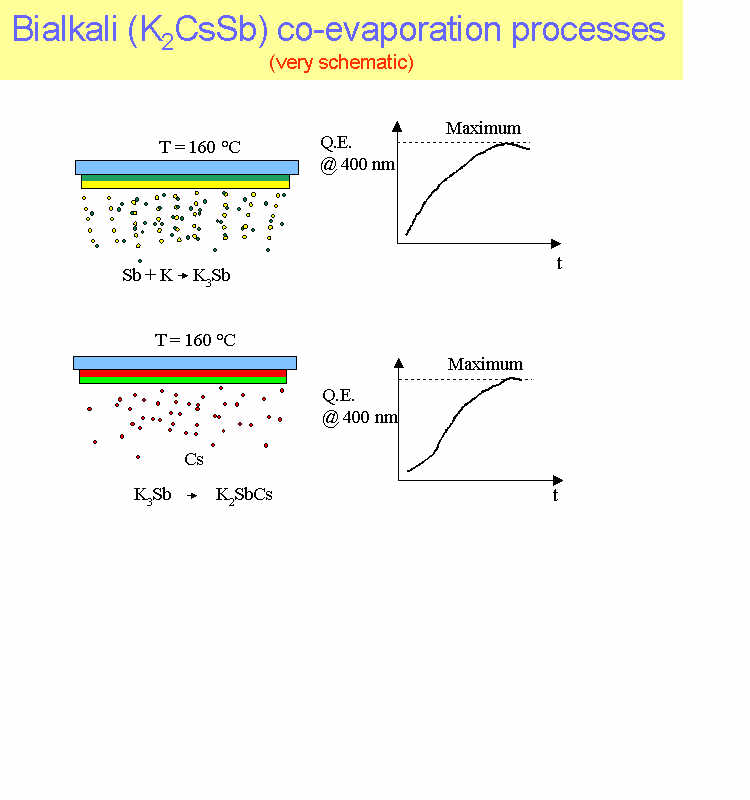
Schematic representation of the bialkali evaporation process
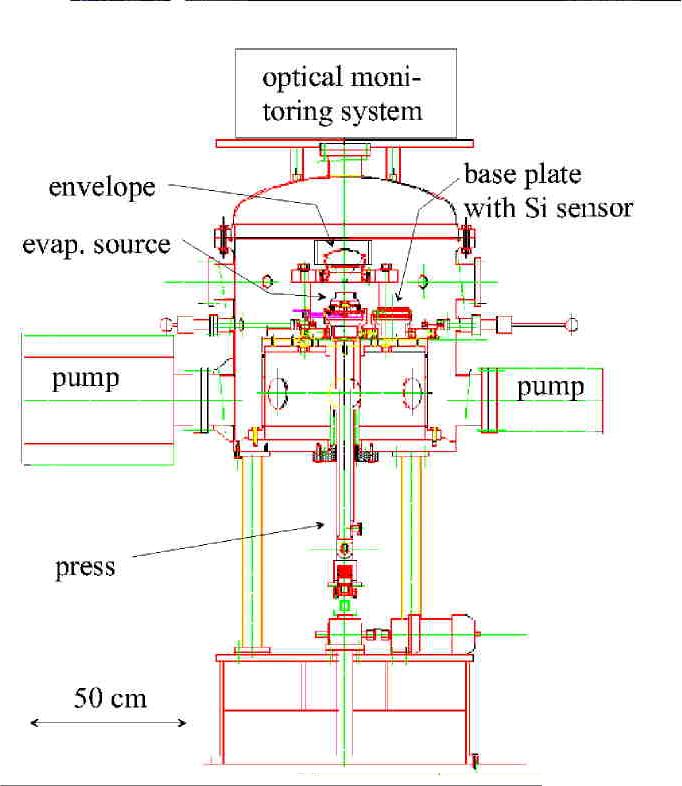
Cross-section of the processing plant
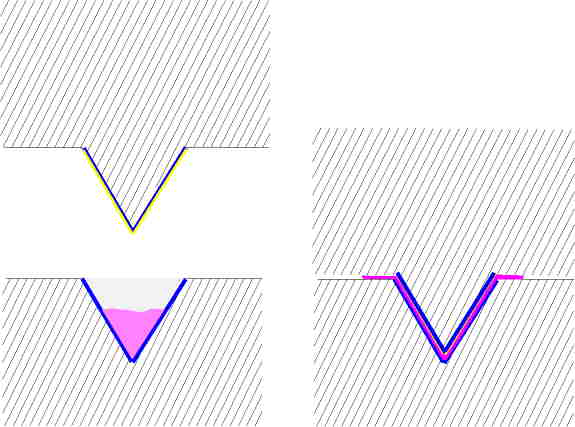
Principle of the cold indium sealing technique |